Colaborações
A equipa procurou desenvolver uma série de parcerias, nomeadamente relacionadas com o desenvolvimento do carro. Este tipo de parcerias permitiram à equipa uma grande aprendizagem e o acesso a uma série de técnicas e meios inovadores da indústria atual.
Instituto Politécnico de Leiria – Escola Superior de Tecnologia e Gestão
A Escola Superior de Tecnologia e Gestão (ESTG) é uma unidade orgânica do Instituto Politécnico de Leiria (IPL) e iniciou a sua atividade em 1989/1990. Além das formações de 1º ciclo (cursos de licenciatura) e de 2º ciclo (cursos de mestrado), da missão da ESTG consta ainda a realização de formações de caráter avançado, a prestação de serviços, a investigação científica e a transferência de tecnologia. Estas são atividades em que a instituição está fortemente empenhada, e que se consubstanciam em projetos e parcerias, sobretudo, com entidades e empresas da região.
A ESTG, nomeadamente o Dr. Nuno Martinho e 2 alunos do curso de Engenharia Mecânica – Anderson Silva e Ruben Estreito – apoiaram a equipa Z-Impulse no desenvolvimento do carro através de testes de aerodinâmica e da maquinação do carro numa máquina CNC existente na escola.
GECO
GECO é uma empresa especializada no fabrico de moldes de injeção para a indústria de plásticos. Esta empresa dedicasse à fabricação e comercialização de moldes de injeção para termoplásticos, bi-componentes e injeção assistida a gás, no âmbito das indústrias automóvel, eletrónica, embalagem, farmacêutica e equipamentos domésticos. Também é Vocacionada para a inovação tecnológica de veículos, com a unidade , FUTI – Indústria de Veículos Automóveis, Lda (tendo como objetivo a criação de um veículo movido a energia alternativa, com um design inovador e utilizando o plástico como principal matéria-prima).
A parceria realizada entre a GECO e a nossa equipa, tem como base, o acesso às novas técnicas do mundo da industria, nomeadamente relativamente à prototipagem. A GECO ajudou-nos na fabricação das rodas, aplicando técnicas avançadas.
ISICOM
A ISICOM é uma empresa vocacionada para soluções CAD/CAM, engenharia e automação industrial.
Devido ao facto de ter profissionais especializados no SolidWorks, esta empresa apoiou a equipa na concepção e fabricação dos aerofólios traseiro e dianteiro, imprimindo o produto final numa impressora 3D.
Desenvolvimento
Veja as fases de desenvolvimento do nosso carro!
Fases de Desenvolvimento:
-
Elaboração de um trabalho de pesquisa, para que possa reunir todos os dados necessários para a construção do carro;
-
Elaboração Esboços;
-
Desenvolvimento do carro em CAD;
-
Realização de Testes Aerodinâmicos;
-
Melhoramento do modelo em CAD conforme os testes aerodinâmicos;
-
Conversão do ficheiro para software CAM;
-
Maquinação do Carro em CNC;
-
Produção dos vários Componentes;
-
Acabamentos;
-
Corrida;
Alguns Fundamentos Teóricos e Pesquisas
Efeito Coandă
tendência de um fio de um fluido (seja ele liquido ou gasoso) permanecer unido a uma superfície curva adjacente. No contexto do projeto: Ao criar uma superfície curva adjacente (superfície convexa), o ar vai circular junto à carroçaria. Assim, não existe dispersão e o ar circula rente ao carro, evitando perturbações e remoinhos.
Princípio de Bernoulli:
O princípio de Bernoulli afirma que para um fluxo sem viscosidade, um aumento na velocidade do fluido ocorre simultaneamente com uma diminuição na pressão ou uma diminuição na energia potencial do fluido. Isto é: Um aumento na velocidade de qualquer líquido ou gás é sempre acompanhado por uma diminuição da pressão.
Atrito
A força de atrito aumenta com o aumento do peso do carro. Quanto mais rugosas as superfícies de contato, pista e rodas, maior o atrito. Assim, a equipa concluiu que o material para as rodas deveria ser o menos rugoso possível. A Equipa procurou então, um material liso, para que o atrito seja mínimo.
Botija
Dados da botija:
-
Peso: 25 a 30g (aproximadamente);
-
Fluxo de massa: 0,28kg/s
-
Massa de CO2: 8g
-
Pressão do CO2: 7 a 8 Mpa
-
Tempo de Propulsão: 0,6 a 0,8s
Rolamentos
Um rolamento é um dispositivo essencial para um movimento rápido do carro. Os rolamentos permitem o movimento relativo controlado entre duas superfícies e servem para substituir a fricção de deslizamento entre estas duas. Neste caso, as superfícies em causa são: os eixos e a roda. Como o atrito é muito menor, a roda fica com um movimento mais prolongado. Os benefícios dos rolamentos cerâmicos, comparados com os de aço, são que os primeiros têm uma superfície mais lisa, logo a rotação é mais durável e assim o carro consegue manter a velocidade. Esta durabilidade é cerca de +25% comparado com os rolamentos de aço. Os rolamentos totalmente cerâmicos seriam ideais, no entanto a sua aquisição seria difícil devido aos custos. Assim a equipa optou por comprar rolamentos em aço, com esferas cerâmicas.
Dos esboços ao Produto Final
Esboços e Maquetas
Os esboços do carro em 2D a várias perspetivas são o primeiro passo para o desenvolvimento do protótipo. Nesta fase os engenheiros da equipa desenharam vários carros, e alternativas para diferentes partes do carro. Além dos esboços em papel, a equipa modelou, através de pasta de moldar, modelos de carros. Estes desenhos e maquetas têm como base fundamentos teóricos, e algumas leis da física e da aerodinâmica. Assim, aperfeiçoa-se o tamanho e as formas do carro.Tivemos como base o carro da equipa Time Flies Racing Team como base.
Principais objetivos nesta etapa:
-
Criar uma menor área frontal do carro, e com uma forma suave para criar um coeficiente de penetração da forma do carro (CX), o mais baixo possível;
-
Conceber um carro cuja a forma consiga equilibrar o máximo possível as forças geradas pela deslocação do carro - a vertical descendente (downforce) e a vertical ascendente (lift). A resultante destas duas forças deve ser nula, para criar uma sensação de voo.
-
Reduzir a área frontal da roda em contacto com o fluido (ar). Como a roda está em permanente rotação durante a corrida, se esta não estiver protegida, iria criar perturbações e remoinhos que iriam prejudicar o desempenho do carro. Também por esta razão, a equipa optou pelas medidas mínimas do rolamento da roda.
-
Na zona inferior do carro, tentou-se criar uma forma que fizesse com que o ar, ai presente, se desloque para as laterais. Isto faz com que a quantidade de ar a embater na roda traseira diminua, evitando perturbações.
CAD
Após a criação das ideias e de passadas para o papel, o passo seguinte é modelar o carro tridimensionalmente. Para tal, utiliza-se o sistema CAD (computer aided design), que no nosso caso foi o SolidWorks. Além do CAD mecânico de fácil aprendizagem, o SolidWorks também oferece uma variedade de produtos de simulação e de realização de testes aerodinâmicos (simulação de fluidos, testes de drag and lift). Além disso também permite a realização de renderizações.
Testes Aerodinamicos
Construímos as várias opções de carros esboçados. Com a realização de testes aerodinâmicos, escolheu-se as características mais vantajosas. Em termos de inovação em teste, utilizamos o modo video para ver o comportamento do seu comportamente real. Mas para isto, não nos era possivel sem as máquinas que filmam em Slowmotion da Casio Exilim!
Sistema CAM
Depois de concluído o projeto do carro em CAD, segue-se a maquinação do carro. Mas antes é fundamental a utilização de um sistema CAM (Computer Aided Manufacturing). A nossa equipa usou o QuickCAM3D. Este software calcula o caminho da ferramenta, a partir da representação geométrica da peça, disponível na forma computacional. Além disso, o QuickCAM3D permite a simulação da trajetória da prototipagem. Com essas duas funções citadas é possível obter com boa precisão do tempo principal da operação.
Para poder maquinar o carro, e utilizar o sfotware CAM é necessário converter o ficheiro de solidworks para STL. Depois, no software, coloca-se o carro conforme o eixo da máquina. A maquinação do carro deve-se processar do plano da botija (ponto do zero físico – localiza-se no plano do furo da botija e no centro do mesmo furo) para a frente, para que não haja colisão com o sistema de fixação, evitando assim possíveis erros de maquinação. Após estes passos é possível dar ordem ao programa CAM para o envio da trajetória da ferramenta e do acionamento da máquina CNC.
Maquinação do Carro
A maquinação do corpo do carro foi feita através de uma maquina CNC -Computer Numerically Controlled - uma máquina semiautomática que permite manufaturar processos de desenho CAD com grande grau de precisão e acabamento. A máquina CNC traz imensas vantagens entre as quais a diminuição do tempo de maquinação.
Para a maquinação do modelo final foi decido que iria ser maquinado na Roland MDX 650, uma máquina com 4ºEixo (rotação do bloco de balsa) de forma a maquinar o corpo nas 4 faces. O software utilizado para elaborar o percurso de maquinação foi utilizado o programa de maquinação da Roland, o Modela Player 4. Este software permite a utilização de ficheiros neutros elaborados em CAD. Associado a este software temos o Virtual Modela, que nos permite observar em 3D o resultado final do percurso de maquinação.
Já com o modelo (balsa) configurado com as orientações corretas, procedemos à elaboração da primeira operação de maquinação, consistindo num facejamento do bloco com o intuito de eliminar as irregularidades que o material possa apresentar. Para esta operação foi utilizada uma ferramenta de 10mm de diâmetro com topo raso, a rodar a 6000rpm e com um desbaste de 1mm. Em seguida adicionamos uma nova operação de maquinação, neste caso o desbaste para começar a delinear a forma do objeto. Teve como parâmetros a mesma ferramenta de corte de 10mm de diâmetro (topo raso), a mesma rotação, um desbaste de 1mm por passagem e uma margem para acabamento de 0,5mm (ou seja deixou 0,5mm acima da dimensão final do objeto).
O Facejamento e o Desbaste foram feitos primeiro na face superior do carro. De seguida com o auxílio do 4ºEixo deu-se a rotação a 90º e foi feito os mesmos dois processos para a face lateral. Deu-se novamente a rotação para a maquinação da face inferior, e novamente a rotação, para a outra face lateral. Para finalizar adicionamos a operação de maquinação nomeada de semi-acabamento. Esta operação consistiu num desbaste ainda mais detalhado, utilizando uma fresa com o diâmetro de 4mm de topo esférico. A nível de parâmetros a rotação foi de 9000rpm, reduziu-se o desbaste máximo para 0,5mm por passagem, retirando-se a margem de acabamento. O intervalo entre trajetórias também foi reduzido para 0,1mm. Nesta operação a máquina-ferramenta vai maquinar até às dimensões finais pretendidas para o objeto.
Mais uma vez usamos o 4ºEixo para a rotação do bloco e acabamento das várias faces. Mas para que o carro esteja pronto é necessário passar pela última fase: o acabamento.
Acabamentos
Os carros são lixados com lixa 280 e 400 para regularizar a superfície da madeira antes da aplicação de qualquer produto. Seguidamente, são aplicadas 2 a 3 demãos de uma base aquosa para madeira. Depois de secos, os carros são novamente lixados com lixa 280 e 400 até ficarem com a superfície lisa. Depois são aplicadas 3 camadas de um primário universal cinzento, capaz de receber qualquer tipo de tinta. A superfície é novamente lixada com grão 400 e finalmente 800 até a superfície ficar perfeitamente lisas. A pintura faz-se com Spray Madeifix laranja em 2 camadas no corpo do carro. Seguidamente isolam-se as zonas a pintar em azul e aplica-se o mesmo tipo de tinta também em 2 camadas.
Impressão 3D
No caso dos aerofólios, das rodas e do nariz do carro a prototipagem foi feita através de uma impressora 3D [3D Systems ProJet TM HD 3000]. Esta impressora tem um grande nível de precisão, ideal para uma produção rápida e eficaz. Isto deve-se ao método usado: Foto polimerização através de raios UV. O material usado é um fotopolímero, ou seja um polímero que altera as suas propriedades quando expostos à luz, neste caso ultravioleta. O polímero utilizado pela equipa foi o EX200 Plastic.
Para executar uma impressão, a máquina lê o desenho de um arquivo STL. E estabelece camadas sucessivas de gel para construir o modelo de uma série de seções transversais. Estas camadas, que correspondem às secções transversais virtual a partir do modelo de CAD, são unidas automaticamente para criar a forma final. A espessura da camada utilizada foi de 37μ.
No final foram feitos os acabamentos, primeiramente com o primário e de seguida a pintura.
Porquê a utilização deste método e deste material?
A zona frontal, do aerofólio dianteiro, é uma a zona de embate com a toalha durante a travagem do carro. Como a balsa é um material muito frágil, além de não suportar espessuras tão finas, iria partir-se. Assim apontámos por um material mais denso e rígido.
Torneamento das Rodas
Inicialmente na escolha do material das rodas, nós tivemos 2 tipos de materiais em mente. Foram eles o plástico e a grafite. Fizemos vários estudos tendo em conta a sua densidade e o seu coeficiente de atrito e acabamos por escolher o plástico devido à sua baixa densidade comparado com a grafite. Através da nossa experiência com o plástico (já que as rodas do carro da final regional tinham sido feitas de ERTACETAL C, um poliacetal) e de todos os estudos que fizemos optamos pelo TIVAR 1000, um polietileno. O principal factor para a escolha deste plástico foi a sua baixa densidade (0,93 g/cm3), sendo este um valor bastante bom. Por outro lado, o TIVAR 1000, embora não tenha o coeficiente de atrito mais baixo de todos os plásticos, apresenta mesmo assim um valor de coeficiente de atrito baixo que anda próximo dos 0,20, um bom valor. Assim, a roda deste material faz com que o carro não seja tão afectado pela força de atrito comparado com os materiais com maior coeficiente de atrito.
Na prototipagem das rodas, a técnica usada foi o torneamento. Este processo, que se realiza através de um torno, consiste na combinação de dois movimentos: rotação da peça e movimento de avanço da ferramenta. Optamos por este tipo de processo devido à qualidade e baixo custo da peça como também devido ao tempo que a peça demora a ser maquinada.
No nosso caso, o torno usado foi o torno cnc pois este é mais vantajoso que o torno mecanico a nível de acabamento e de tempo de produção. Esta máquina diferencia-se das outras pois a maquinação da peça é feita por Comandos Numéricos Computadorizados (CNC) através de duas coordenadas (X e Y). A peça encontra-se estacionária e vai sendo cortada pela ferramenta de corte que descreve movimentos em dois eixos (X e Y). Para colmatar o facto da ferramenta nao descrever movimentos no eixo Z, a peça realiza movimentos rotacionais. Assim, a peça vai adquirir tamanhos cada vez menores que o tamanho inicial até obter a forma desejada.
Renderizações Finais
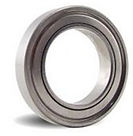


Logotipo do patrocinador de Rolamentos
Rolamento usado

Esboços do carro
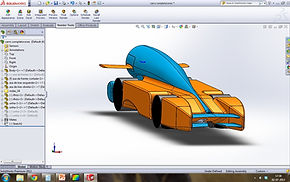
Software CAD - Solidworks
Teste SlowMotion
Patrocindado por Casio Exilim

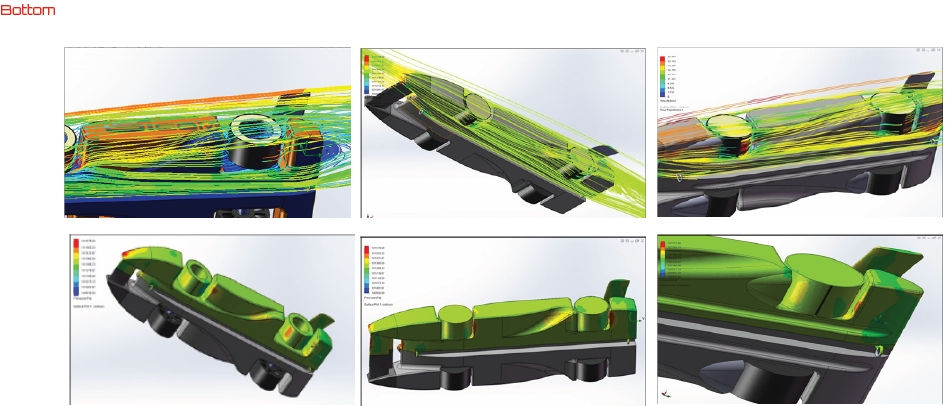


Testes Aerodinamicos em Solidworks

Software CAM
Maquinação do Carro no Centimfe
![]() |
---|
![]() |
![]() DSC02065.JPG |
![]() DSC02067.JPG |
Acabamentos
![]() |
---|
![]() |
![]() |
![]() |
![]() |
![]() |
![]() |
![]() |
![]() |
![]() |
![]() |
Peças Prototipadas
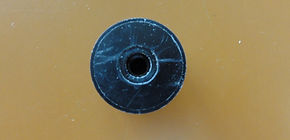
Roda Torneada
![]() | ![]() | ![]() |
---|---|---|
![]() | ![]() | ![]() |
![]() | ![]() | ![]() |
![]() | ![]() | ![]() |
Agradecimentos
Queremos expressar os nossos agradecimentos a todos aqueles que, de algum modo, contribuíram para a investigação e produção do carro da nossa equipa.
Primeiramente aos alunos do curso de Engenharia Mecânica na ESTG, Anderson Silva e Ruben Estreito, pela fantástica colaboração na maquinação do carro. Depois aos professores da ESTG, Dr. Nuno Martinho e Dr. Pedro Martinho pela disponibilidade e apoio mais técnico e ao professor Paulo Roldão por nos acompanhar e ajudar no projeto, embora não participando no mesmo este ano. Por fim, ao nosso professor coordenador José Carlos Mendes, que foi incansável, e apoiou a equipa em todo o processo de conceção do carro.
Patrocinadores
![]() |
---|
![]() |
![]() |
![]() |
![]() |
![]() |
![]() |
![]() |
![]() |
![]() |
![]() |
![]() |
![]() |
![]() |
![]() |
---|